Transferring a Pattern
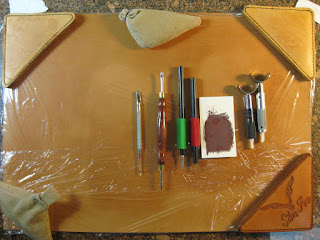
Some years ago, because my leather dried too quickly, I needed to figure out an option to maintain a working moisture content in the leather for longer. If leather is wet and allowed to dry too often it becomes harder, literally tougher to cut and tool. Because of this I decided to try covering the leather with plastic to retain the moisture. After trying several kinds of plastic, I settled on cling wrap, any brand. Because it is so thin and strong I can case the leather, cover it with the plastic and when it's ready for transferring a design, put the paper pattern right on top and trace away. My pattern doesn't fall apart because of the moisture and the lines remain crisp and clean. I can feel an indentation on the paper with my finger where the tracing is already done or lift and look if necessary. Tracing film works well but because of the thickness the lines transferred tend to be wide and blur when put close together. Another little time saver is to use a modeler right ove...